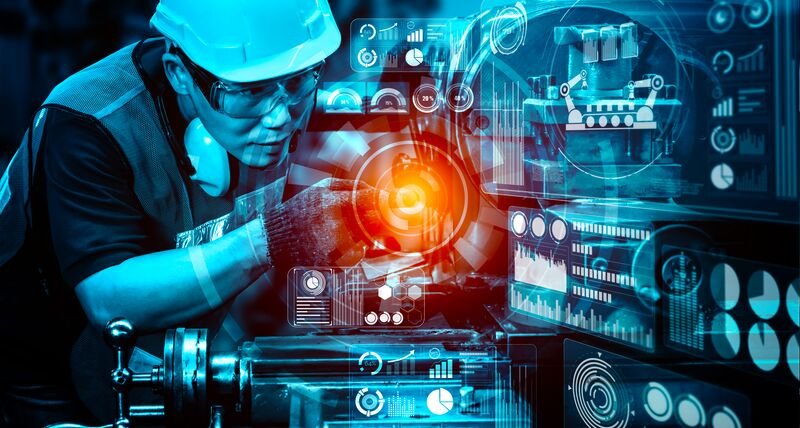
OVERVIEW
The Predictive Maintenance System empowers organizations to monitor equipment health proactively, preventing operational failures. By leveraging advanced predictive algorithms and real-time data from equipment sensors, it estimates potential failure timelines, identifies root causes in complex machinery, and determines which components require repair or replacement. This approach minimizes unplanned downtime and extends equipment lifespan.
The system employs condition monitoring techniques to track critical machinery parameters, such as vibration and temperature, detecting significant changes indicative of potential faults. Scheduled maintenance actions can then be executed strategically, preventing secondary damages and mitigating operational risks.
Data collected through the system enables trend analysis, failure prediction, and accurate calculation of an asset’s remaining useful life. This breakthrough in vibration monitoring technology complements traditional analysis methods, offering early detection of challenging machine issues, including gear and bearing damage, which are often undetectable with conventional techniques. By integrating this advanced solution, organizations can enhance operational efficiency, optimize maintenance schedules, and maximize asset performance
KEY FEATURES OF PREDICTIVE MAINTENANCE SYSTEM
- Condition Monitoring: Tracks critical parameters like vibration and temperature to detect potential faults.
- Strategic Maintenance: Facilitates timely maintenance actions, preventing secondary damage and reducing risks.
- Trend Analysis: Enables failure prediction and calculates an asset’s remaining useful life.
- Advanced Vibration Monitoring: Detects hard-to-identify issues, such as gear and bearing damage, improving upon traditional methods.
OPERATIONAL BENEFITS
- Minimizes unplanned downtime, ensuring smooth operations.
- Extends equipment lifespan, reducing overall maintenance costs.
- Supports optimal asset utilization and operational efficiency.
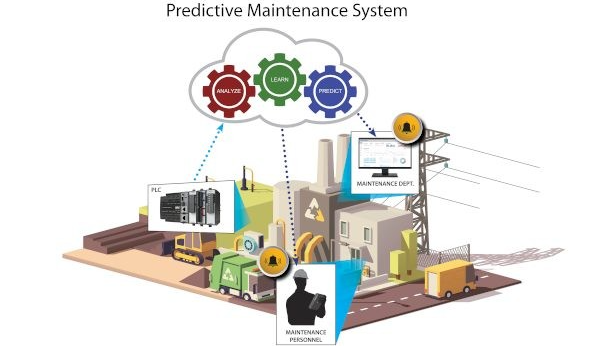
OBJECTIVES OF CONDITION-BASED MAINTENANCE (CBM)
The primary objective of Condition-Based Maintenance (CBM) is to optimize maintenance resources by ensuring maintenance activities are carried out only when necessary. Leveraging advanced predictive maintenance tools, CBM facilitates the detection, monitoring, analysis, and identification of anomalies in machinery, enhancing operational reliability and efficiency.
VIBRATION MESSUREMENT TECHNIQUES
CBM employs two distinct vibration measurement methods, chosen based on the criticality and operational priority of the equipment:
- Permanent Online Vibration Monitoring Systems
- Continuous, real-time monitoring for high-priority or critical equipment.
- Ideal for detecting anomalies promptly and ensuring uninterrupted operations.
- Portable Offline Vibration Monitoring Systems
- Periodic monitoring using portable equipment for less critical assets.
- Cost-effective for equipment with lower operational significance.
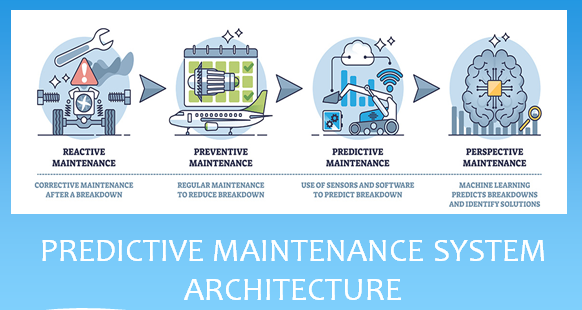
FUNCTIONAL SPECIFICATION FOR PREDICTIVE MAINTENANCE SYSTEM
- Real-Time Monitoring: Tracks critical parameters like vibration and temperature for anomaly detection.
- Predictive Analytics: Forecasts potential failures and calculates remaining useful life (RUL).
- Condition Monitoring: Utilizes advanced diagnostics like oil analysis and thermal imaging.
- Optimized Scheduling: Automates maintenance planning to reduce downtime and costs.
- Data Management: Supports secure data storage, analysis, and API integration.
- User-Friendly Interface: Provides intuitive dashboards and mobile apps for insights.
- Scalability: Supports multiple sensor nodes and integrates with enterprise systems.
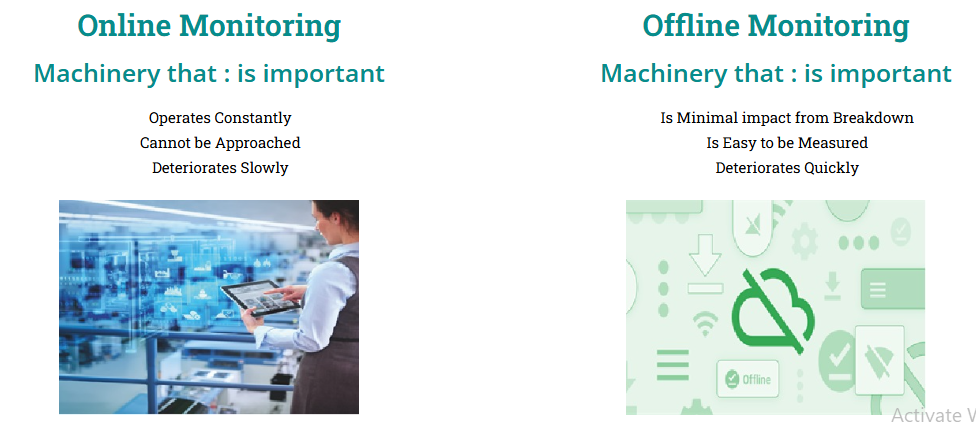
CHALLENGES FACED BEFORE IMPLEMENTING PREDICTIVE MAINTENANCE SYSTEM
- Frequent Equipment Failures- Reactive maintenance approaches result in unexpected breakdowns, disrupting operations and escalating repair costs.
- Unplanned Downtime- Lack of early warning systems leads to operational interruptions, impacting productivity and revenue.
- Inefficient Maintenance Practices- Scheduled maintenance often results in over-maintenance or under-maintenance, wasting resources and increasing risks.
- Inadequate Fault Detection- Traditional monitoring techniques fail to identify early-stage issues, such as gear or bearing damage, leading to secondary failures.
- High Maintenance Costs- Emergency repairs, unscheduled interventions, and inefficiencies inflate overall maintenance expenditures.
- Limited Asset Lifespan- Failure to monitor critical parameters like vibration, temperature, and oil quality reduces equipment durability and performance.
- Data Silos- Fragmented systems hinder effective data collection, analysis, and actionable insights, limiting maintenance optimization.
- Reactive Approach to Failures- Absence of predictive analytics results in a reliance on corrective measures after faults occur, increasing downtime.
- Resource Overuse- Excessive reliance on spare parts, consumables, and manual interventions due to inefficient maintenance cycles.
- Missed Cost-Saving Opportunities- Inability to analyze trends and optimize schedules prevents organizations from reducing operational and maintenance costs.
- Operational Safety Risks- Undetected anomalies and delayed maintenance actions jeopardize workplace safety and compliance with industry standards
OUR SOLUTION
Standalone Compact CBM System
- A self-contained solution designed for streamlined condition-based monitoring, offering the following features:
- Gateway Connectivity: Utilizes Bluetooth technology for seamless interaction with the gateway.
- Power Supply: Battery-operated for flexible deployment.
- Gateway Interface: Supports Ethernet connectivity for data transfer.
- Sensor Capability: Supports up to 256 sensor nodes for comprehensive monitoring.
- API Integration: APIs available for system integration and customization.
- Cloud and On-Premises Support: Data storage options tailored to organizational needs.
- Easy Installation: Simple stud mounting for quick setup.
- Remote Firmware Updates: Over-the-air firmware upgrades for effortless system enhancement.
- End-to-End Solution: Combines software and hardware in a single package.
- User-Friendly Interface: Mobile application and dashboard functionality for real-time insights.
- Advanced Analytics: Includes features like waterfall analysis and machine downtime tracking.
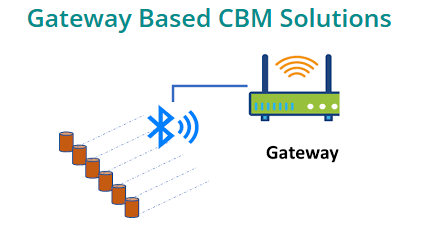
Controller-Based CBM Solution
A robust system tailored for high-performance applications, offering:
- Customizable Sensors: Includes probe-type sensors to meet specific requirements.
- Scalable Sensor Network: Cabled sensors extendable to suit operational needs.
- High-Performance Monitoring: Designed for environments with elevated temperature and vibration levels.
- Reciprocating Machinery Support: Addresses unique needs of reciprocating applications.
- Specialized Software: Requires dedicated online or offline software for monitoring and analysis.
- Comprehensive Hardware: Includes a controller and associated accessories for a complete solution.
How Predictive Maintenance Operates
Predictive maintenance leverages historical and real-time operational data to proactively identify potential issues before they occur. It integrates multiple aspects of organizational processes to ensure seamless anticipation and prevention of failures. The primary components influencing predictive maintenance include:
- Real-Time Asset Monitoring
Continuous tracking of asset conditions and performance to detect anomalies. - Work Order Analysis
Examination of historical maintenance data to identify patterns and optimize future actions. - MRO Inventory Benchmarking
Assessment of maintenance, repair, and operations inventory usage to enhance resource planning and efficiency.
Core Elements of Predictive Maintenance
Technology and software play a pivotal role in predictive maintenance. Advanced tools such as the Internet of Things (IoT), artificial intelligence (AI), and integrated systems enable seamless connectivity, collaboration, and data sharing across various assets and operations.
Predictive maintenance technologies capture data using specialized sensors, industrial controls, and business systems. These tools process and analyze the data, generating actionable insights to address potential issues.
Key Predictive Maintenance Techniques
Examples of predictive maintenance methodologies include:
- Vibration Analysis: Detects early signs of mechanical failure.
- Oil Analysis: Monitors lubrication quality and identifies contamination.
- Thermal Imaging: Identifies heat patterns indicative of potential problems.
- Equipment Observation: Tracks operational behaviors to pinpoint irregularities.
Cloud-Based Predictive and Prescriptive Maintenance
Our Industrial Internet of Things (IIoT) solutions empower organizations with advanced predictive and prescriptive maintenance strategies, ensuring optimal performance for critical industrial assets.
Real-time mechanical, thermal, and electrical data is captured through cutting-edge sensors. Advanced analytics identify trends and generate alerts, enabling proactive action before equipment failure occurs.
Predictive Maintenance is best suited for simpler systems, where a single variable can effectively predict potential failures. In contrast, Prescriptive Maintenance is applied to more complex systems, where multiple variables are analyzed to forecast failure. This approach demands a deeper understanding of operating conditions and offers a more precise diagnosis, reducing the likelihood of false positives.
BENEFITS OF PREDICTIVE MAINTENANCE
When implemented effectively, predictive maintenance ensures that maintenance activities are conducted only when necessary—right before a failure is likely to occur. This targeted approach leads to significant cost savings:
- Reduced Maintenance Time: Minimizes unnecessary maintenance interventions.
- Improved Production Uptime: Decreases production downtime associated with unscheduled maintenance.
- Cost Efficiency: Lowers the expenses related to spare parts, supplies, and emergency repairs.
PREDICTIVE MAINTENANCE USECASE
- Rotational Equipment
- Submersible Pump Systems
- Vibration and Acoustic Control
- Heat Transfer Systems
- Rolling Mill Machinery
- Pumping Solutions
- Gearbox Monitoring
- Reciprocating Equipment
- CNC Machine Monitoring
- Conveyor System Optimization
- Boiler Performance Management
- Spindle Motor Monitoring
- Electric Motor Performance
- Induced and Forced Draft Fan Systems
Optimizing Asset Performance Through Predictive Maintenance
Predictive maintenance is a data-driven strategy focused on optimizing asset performance by determining the most cost-effective maintenance intervals. This approach minimizes downtime, enhances reliability, and reduces unnecessary operational costs.
Successful implementation of predictive maintenance relies on the integration of advanced Internet of Things (IoT) technologies. Key components include the use of sophisticated monitoring tools such as vibration analysis, oil condition monitoring, thermal imaging, and real-time equipment performance tracking, enabling early issue detection and proactive maintenance to ensure operational continuity and efficiency.
CONCLUSION
Raygain continues to lead the way in the field of predictive maintenance, offering cutting-edge solutions that empower organizations to optimize asset performance and drive operational efficiency. With our advanced, data-driven approach and seamless integration of Internet of Things (IoT) technologies, we provide a comprehensive suite of tools that minimize downtime, extend equipment lifespan, and reduce maintenance costs. Our innovative predictive maintenance systems, backed by state-of-the-art vibration analysis, thermal imaging, and real-time monitoring, enable organizations to take proactive measures, ensuring maximum reliability and efficiency across their operations. By choosing Raygain, businesses can stay ahead of potential failures, enhance their maintenance strategies, and achieve sustainable growth and performance excellence.