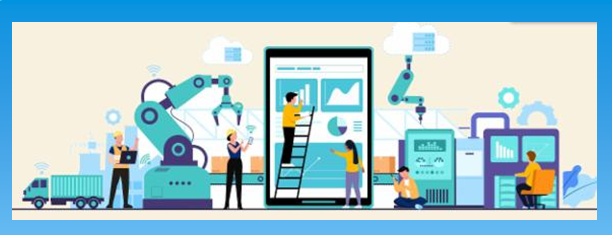
OVERVIEW
A Production Management System (PMS) serves as a cornerstone for driving operational excellence within manufacturing and production-intensive organizations. It is a sophisticated, enterprise-level solution tailored to enhance the efficiency, accuracy, and scalability of production processes. By consolidating critical functions into a centralized platform, a PMS empowers organizations to synchronize production capabilities with overarching business strategies, thereby ensuring sustained competitiveness in dynamic markets.
KEY FEATURES OF PMS
- Strategic Production Planning: Supports advanced scheduling and capacity planning to align production activities with business goals, ensuring on-time delivery and cost efficiency.
- Resource Optimization: Enhances the utilization of assets, including machinery, materials, and labor, reducing downtime and minimizing waste.
- Operational Visibility: Offers real-time monitoring and reporting on production metrics, enabling data-driven decision-making and proactive issue resolution.
- Quality Control Integration: Incorporates quality management protocols to maintain product standards, ensuring compliance with regulatory and customer requirements.
- Cross-Functional Integration: Connects seamlessly with Enterprise Resource Planning (ERP), Supply Chain Management (SCM), and Customer Relationship Management (CRM) systems, fostering a cohesive ecosystem for end-to-end operational excellence.
- Scalability and Adaptability: Provides flexibility to scale operations and adapt to dynamic market conditions or production demands, ensuring business continuity and competitive advantage.
FUNCTIONAL SPECIFICATION FOR PMS
- Display Screen Features:
- Rotating Display: Cycles through data cells every 12 seconds for continuous visibility.
- Line Status Indicator:
- Yellow: No input for 5 minutes (inactivity).
- Green: Line operational.
- Red: Line stopped.
- User Authentication:
- Secure login with user credentials to ensure data integrity and prevent unauthorized access.
- Administrative Control:
- Only admin users can modify REPORT, SETTINGS, CONFIGURATION, and EMAIL modules.
- Report Generation and Export:
- Reports can be generated by selecting a date and exporting via the EXPORT button.
- Email Reporting:
- Reports can be emailed to pre-configured recipients for streamlined communication.
Report Generation Overview
The Production Management System (PMS) supports the generation of key operational reports, including:
- Daily Performance Reports: Detailed daily production analysis.
- Monthly Performance Reports: Executive summaries of monthly KPIs.
- O.E.E. Reports: Evaluation of equipment effectiveness (availability, performance, quality).
- Workforce Utilization Reports: Insights into labor productivity and resource allocation.
- System Utilization Reports: Overview of application performance and user engagement.
- Downtime Reports: Analysis of downtime incidents and their impact.
- Changeover Efficiency Reports: Assessment of changeover durations and optimization opportunities.
- Hourly Production Reports: Real-time production metrics for immediate action.
Strategic Operational Functions
- Production Scheduling and Execution Efficiency:- Real-time production data capture via smart devices for enhanced visibility and operational efficiency.
- Machine Utilization and Downtime Management:- Continuous monitoring of machine utilization, cycle times, and deviations, with automated alerts for machine outages and changeovers.
- Asset Maintenance and Performance Optimization:- Proactive maintenance scheduling and asset usage tracking to extend equipment life and minimize downtime.
- Order Lifecycle Management and Tracking:- Full visibility of orders through seamless integration with SAP, Tally, and Busy, ensuring efficient order management across the shop floor.
- Real-Time Quality Monitoring and Process Control:- Real-time tracking of production quality metrics, enabling effective process control and consistent product quality.
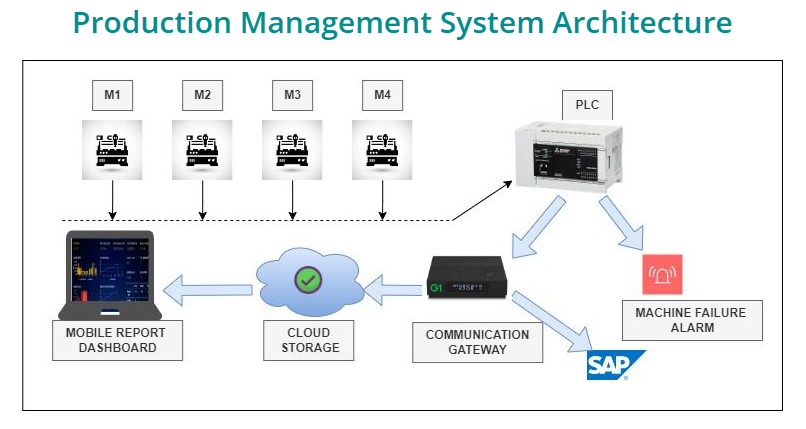
CHALLENGES FACED BEFORE IMPLEMENTING PRODUCTION MANAGEMENT SYSTEM
- Inefficient Production Planning- Manual or fragmented planning processes lead to resource misallocation, delays, and suboptimal scheduling.
- Lack of Real-Time Visibility- Limited access to real-time data hinders informed decision-making and rapid issue resolution during production.
- Operational Silos- Disconnected departments and systems result in poor communication and coordination, reducing overall efficiency.
- High Operational Costs- Inefficiencies in resource utilization, material wastage, and unplanned downtime drive up production costs.
- Inconsistent Quality Standards- Lack of standardized workflows and quality monitoring increases the risk of defective products and customer dissatisfaction.
- Delayed Issue Resolution- Reactive approaches to equipment failures and production bottlenecks lead to prolonged downtime and productivity losses.
- Inaccurate Demand Forecasting- Ineffective integration of sales, inventory, and production data results in overproduction or stockouts.
- Limited Scalability- Traditional systems struggle to adapt to changes in production volume or complexity, restricting business growth.
- Poor Performance Monitoring- Lack of comprehensive reporting and analytics makes it difficult to evaluate productivity, identify inefficiencies, and drive continuous improvement.
- Regulatory Non-Compliance- Difficulty in tracking and documenting processes leads to challenges in meeting industry standards and regulatory requirements.
- Manual Dependency- Excessive reliance on manual processes increases errors, slows operations, and reduces overall productivity.
KEY BENEFITS OF PRODUCTION MANAGEMENT SYSTEM
- Enhanced Equipment Management to improve manufacturing efficiency.
- Optimized Resource Allocation to reduce labor costs.
- Centralized Data Management to eliminate errors and duplication.
- Streamlined Procurement to reduce material costs.
- Improved Planning and Control to reduce work-in-progress times.
- Superior Production Control to ensure consistent output.
- Standardized Procedures for greater operational consistency.
- Faster Accessibility to critical production data.
- Enhanced Monitoring for real-time performance tracking.
- Error-Proofing Mechanisms to increase data accuracy.
- Integrated Systems for seamless operation and full transparency.
- Production Analysis for continuous performance improvement.
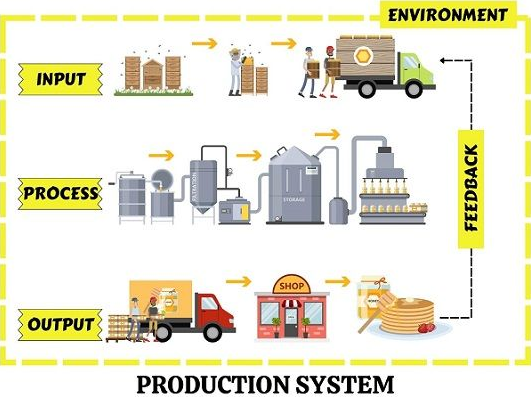
Dynamic Production Line Management Ecosystem
- Efficient Line Status Monitoring
- Bottleneck Identification and Resolution
- Accurate Setup Time Tracking
- IoT-Driven Data Logging
- Graphical Representation of Production Line Layout
- Advanced Machine Vision Technology
- Proactive Maintenance Alerts and Notifications
Machine Runtime Optimization System
- Overall Equipment Effectiveness (OEE) Monitoring
- Data Collection and Integration
- Workforce and Operator Utilization Analysis
- Downtime Impact Assessment
- Daily Efficiency Performance Reporting
Efficiency Monitoring and Analysis Tools
- Real-Time Efficiency Measurement
- Comprehensive Downtime Analysis
- High-Speed Production Tracking
- Cloud-Enabled, Application-Based Monitoring
- Automated Report Generation
Additional Features and Enhancements
- Proactive Alarm and Alert Notifications
- Real-Time Fault Diagnostics and Troubleshooting
- Seamless Wireless Connectivity
- Integrated PLC Server with Advanced Analytics
- Automated Email Notifications
- Machine Vision Technology for Surveillance and Monitoring
CONCLUSION
Raygain’s Production Management System (PMS) exemplifies innovation and excellence in delivering cutting-edge solutions for manufacturing efficiency. By combining advanced technology with seamless integration, PMS empowers businesses to optimize operations, enhance productivity, and achieve strategic goals.
With a focus on quality, scalability, and adaptability, Raygain continues to set new benchmarks in enabling organizations to thrive in competitive markets through streamlined production and data-driven decision-making.